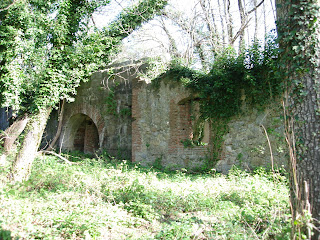
Los "martinetes de cobre" eran industrias destinadas a la fundición y transformación del mineral de cobre utilizando la energía hidráulica. En estas fábricas de fundición se podían distinguirse dos secciones: el área de fundición del mineral en hornos y el forjado y elaboración de los calderos de cobre. Ambas funcionaban con energía hidráulica. Son varios los factores que explican la localización de estas industrias siderúrgica: la presencia de mineral de cobre, la corriente de un río para proporcionar energía y bosques abundantes que suministrasen carbón vegetal. Tanto el mineral como el combustible podían ser transportados desde lugares cercanos, cuanto más próximos mejor, sin embargo el agua no podía desplazarse.
El cobre es uno de los metales que más pronto se conocieron y utilizaron por el hombre, pues se encuentra en la naturaleza en estado nativo, es decir, mostrando sus características metálicas más relevantes. Es dúctil, maleable y suelda fácilmente, lo que permite fabricar muchos objetos de chapa e hilos muy finos. El punto de fusión es relativamente bajo (1.200 ºC) y presenta gran facilidad para formar aleaciones con muchos metales, como el estaño, cinc, plomo, plata, níquel, etc. El proceso de fundición del mineral de cobre era conocido desde la antigüedad. Se utilizaban pequeños hornos y la aireación se conseguía de forma natural (mediante oberturas en las paredes del horno) o forzándolo mediante tubos de soplado o fuelles manuales. Los sistemas de aireación eran fundamentales, ya que a mayor presión el carbón se quemaba rápidamente y se obtenían temperaturas más altas.
Durante la Edad Media se consiguió mecanizar la alimentación del aire a través de unos fuelles o barquines movidos de forma hidráulica, aportando una cantidad constante y suficiente de aire a la fragua. A partir del siglo XVII encontramos otra importante innovación técnica con las trompas de soplado. Ambos sistemas fueron utilizados en las fábricas de cobre de la Cordillera Ibérica. . De hecho, hasta el siglo XVIII las energías básicas utilizadas por el hombre fueron el aire y el agua. Los medios naturales y maquinarias sencillas como los molinos, los batanes y los martinetes aplicados a diferentes producciones era la única tecnología que el hombre tenía a su alcance. Los ingenios de aire y agua.
Una vez triturado y limpio el mineral de cobre se mezclaba con carbón vegetal, se introducía en el horno y se encendía. El horno era una pequeña cavidad con cuatro paredes, normalmente con forma piramidal invertida. Solían ayudarse de fundentes para facilitar la tarea, espolvoreando polvo de cuarzo en las paredes del horno. Cuando el metal empezaba a volverse líquido, las escorias se depositaban en el fondo por su mayor densidad y el metal limpio quedaba en la superficie. De este modo podía ser extraído mediante unas cucharas de hierro y volcado en los correspondientes moldes. Una vez solidificado, el metal era calentado de nuevo y forjado con los martillos para eliminar todos los restos de impurezas.
Los fuelles o barquines era el sistema más difundido para inyectar aire al horno. Fueron utilizados en casi todos los martinetes de la Cordillera Ibérica. Consistían en unos grandes fuelles de cuero y madera movidos por un eje que estaba conectado a la rueda hidráulica. Hacían falta dos barquines para proporcionar aire de forma continua, alternado sucesivamente las tareas de aspiración y expulsión. Exigían un fuerte mantenimiento, ya que necesitaban ser engrasados para evitar los rozamientos y había que reparar continuamente los cueros para evitar pérdidas de aire.
Una vez fundido el cobre había que forjarlo, eliminando a golpe de martillo las impurezas. También había que darle forma, moldeando el metal para conseguir los productos deseados. Para ambas funciones era fundamental el uso de los martillos y yunques.
El martinete movido por energía hidráulica es un invento medieval que se difundió rápidamente por toda Europa. Agilizaba las tareas del forjado y aumentaba los rendimientos, consiguiendo un incremento de la capacidad de producción de las fábricas. Esto provocó un abaratamiento de los costes de elaboración de las calderas de cobre, lo que facilitó en último término la difusión doméstica del producto. Casi todos los hogares se pudieron permitir la compra de calderos de cobre para cocinar, cosa impensable varios siglos antes.

El martinete era un enorme martillo, que podía pesar más de 100 kilogramos, instalado sobre un ingenio mecánico. La energía que movía el gran mazo era transmitida desde una rueda hidráulica a través de un cigüeñal que tenía en su extremo unas levas o cuñas que giraban y que conectaban regularmente con el extremo de una viga de madera o mancha. En el otro extremo estaba fijado el martinete. Cuando giraba el eje, las levas tiraban hacia abajo de la viga, con lo que el martillo se elevaba. Por efecto del giro, la leva soltaba la viga y el martillo caía por su propio peso sobre el yunque. Para facilitar este movimiento, las manchas estaban fijadas al suelo mediante unas bogas. Las vigas de madera de las manchas se desgastaban con bastante facilidad, por lo era preciso protegerlas utilizando badanas de piel cosidas. También era frecuente adobarlas con aceite para disminuir los rozamientos. Debajo del martillo se situaba un enorme tronco de madera, preferiblemente haya, llamado a veces ruejo por su parecido con este utensilio agrícola. Estaba reforzado con hierro en el extremo que recibía el golpe del martillo.

En los martinetes se elaboraban las grandes calderas domésticas que encontramos en algunas casas. Era conveniente que todas estas calderas no llevasen soldaduras para garantizar la estanqueidad, por lo que su elaboración exigía un proceso técnico que sólo podía realizarse en los propios martinetes. Se fundía el metal hasta hacerse líquido y se volcaba en un molde semicircular, creando una copa maciza. Una vez enfriado, se extraía la pieza, se calentaba hasta quedar al rojo vivo y se martilleaba el interior con mazos apropiados hasta que adquiría la forma de plato sopero con las paredes muy gruesas. Se enfriaba en agua para templar el cobre. Se volvían a calentar en la fragua y a golpear, repitiendo varias veces la operación hasta que se conseguía la forma adecuada. Cuantos más golpes recibían y más se estrechaban las paredes, más grande se hacía el utensilio. Si el molde donde se volcaba el metal fundido era plano y los golpes del martillo se repartían de forma homogénea por toda la superficie, el resultado final era una plancha metálica. Estas planchas eran posteriormente vendidas a los artesanos caldereros, quienes las recortaban mediante plantillas, las doblaban y soldaban, elaborando pequeños utensilios.

Los calderos han sido recipientes metálicos preferentemente de cobre, grandes y redondos utilizados para calentar o cocer alimentos depositados en su interior y de uso generalizado en los hogares o fuegos bajos de las viviendas. Fueron imprescindibles en todas las cocinas que precisaban al menos de un caldero principal, además de otros complementarios de diversos tamaños y usos. Comenzaba el proceso fundiendo trozos de chatarra, de cobre de todo tipo, en un crisol cerámico en el que se mezclaban en capas alternas el carbón vegetal y el metal. Una vez conseguida la fusión del cobre y a una temperatura que por experiencia el calderero sabe que es la adecuada, lo que conoce por el color, se sacaba el líquido a mano con un cazo provisto de un largo mango y se vertía en unos moldes de barro refractario dispuesto en el fogón y en los que solidificaba tomando su forma de casquete cuyo tamaño variaba (siendo los menores de 10 o 12 centímetros de diámetro) en función del peso de los calderos a obtener. Cuando aún los trozos de cobre se encontraban calientes, se los cogía con unas tenazas y se los llevaba al martillo hidráulico que dispone de un yunque o chabota con su superficie ligeramente cóncava, donde el calderero martillador sentado sobre un taburete junto al mazo y sujetando con sus manos la pieza de cobre caliente por medio de sendas tenazas cerca de sus pies bajo el martillo, la iba sometiendo a continuos y repetidos golpes mientras la desplazaba ligeramente entre uno y otro. Como consecuencia, la pieza se iba adelgazando y aumentaba su extensión al mismo tiempo que iba tomando, golpe tras golpe, la forma cóncava característica de los calderos.

Cuando la lámina alcanzaba un determinado espesor mínimo y para evitar su rotura por efecto de los golpes, se introducía en el primer caldero otro de iguales dimensiones y el martillador iba adelgazando las dos piezas y conformándolas simultáneamente. Esta operación era repetida sucesivamente a medida que el espesor conjunto de las piezas se iba reduciendo llegando a manipular hasta 9 calderos a la vez agrupados en forma de paquete, de forma que quedaban finalmente por efecto de los numerosos golpes, con un espesor de pared de 1,5 milímetros cada uno de ellos. El trabajo de martillador requería habilidad y experiencia para ir moviendo el cuenco con las tenazas. La postura en que debía trabajar y el esfuerzo necesario unido al ambiente, hacían que su tarea fuera especialmente penosa. Por efecto de las deformaciones a que era sometido, el cobre se iba endureciendo por lo que era preciso recocerlo, calentándolo en la fragua para reducir su resistencia y poder trabajarlo adecuadamente. Una vez limpios se pasaba a darle la forma definitiva, golpeándolos con martillos de mano (rebatido), que corregían las deformaciones no deseadas producidas por la maquina hidráulica y que así mismo dejaban sobre toda su superficie las características y numerosas marcas de sus golpes. Terminaban su fabricación rodeándolo con un aro de hierro también forjado a mano y colocándole una o más asas del mismo material.

La existencia de energía barata, agua y carbón vegetal, explica la existencia de un Martinete de cobre en El Barranco y concretamente dentro de la jurisdicción de la Villa de Mombeltrán. Si a estos factores le sumamos el conocimiento de la mano de obra materializada en aquellas migraciones, circunstancia que se produce durante la repoblación de las tierras del Tietar durante el proceso de la Reconquista de las tierras al sur del Duero, y que como sabemos aquellos pobladores procedente del norte de la península conocían desde tiempo esta industria de transformación del cobre.
Las ruinas de lo que fue el primitivo Martinete se encuentran como a unos dos kilómetros de Mombeltrán, aguas abajo del río Ramacastañas y en su margen derecho en un espacio comprendido entre el cauce del río y la Cañada Real Leonesa Occidental. A corta distancia de lo que fue el Martinete se encuentra el despoblado de Arroyo Castaño, hoy reducido a las ruinas de su antigua parroquia, algunos restos de antiguas edificaciones y un puente, así como una antigua posada de arrieros y pastores que se conserva en un aparente buen estado de conservación.
No olvidemos la importancia que durante el siglo XV tenía Arroyo Castaño, cuya existencia se halla documentada en 1462. Arroyo Castaño tuvo una gran relevancia cuando el rey Enrique IV traslado los derechos de portazgo a este sitio procedentes de Ramacastañas a fin de beneficiar a su valido D. Beltrán de la Cueva. Allá por el año 1845 contaba con 20 casas habitables, taberna, parroquia, y una fabrica de tinajas. Además existían dos martinetes y un molino harinero.
El martinete que nos ocupa estaba techado, tenía dos fraguas y junto a él había una casa con dos plantas destinada a la vivienda del martinetero. Disponía de dos pares de fuelles grandes con tobera de cobre, de dos “machos” de hierro con las bocas de acero y dos bocas grandes de hierro en las que daba el macho, un yunque, varias tenazas para calentar y encopar, varios martillos, balanzas, tijeras para cercenar, muchos moldes…Los machos se movían por la fuerza del agua que una acequia sacaba de la pesquera del río y que un caz (canal para coger el agua y conducirla hasta el lugar donde será utilizada) hecho de piedra hacía llegar al martinete. Las fraguas se calentaban con carbón vegetal hecho de madera de pino, roble o brezo que se adquiría al concejo de la villa.

Una profesión profundamente ligada a la industria del hierro fue la de carbonero. Quedan aun algunos vestigios que nos hablan de aquella actividad. Bajo el puerto del Arenal y en Las Morañegas existieron frondosos bosques de robles y castaños con los que se hacía el cisco y carbón para las fraguas y martinetes. El camino llamado de Carboneros aun conserva a duras penas su enlosado de piedra y existe un pago llamado La Peguera que determina el lugar en donde se fabricaba el carbón vegetal.
El carbonero desarrollaba un trabajo muy duro bajo situaciones meteorológicas de todo tipo. Durante la elaboración del carbón no había tiempo para el descanso ni el sueño. Tanto de día como de noche el carbonero debía controlar varios hornos que se encontraban en diferentes fases del proceso, lo que exigía una vigilancia continua. La preparación de la leña dependía de su tipo y del lugar dónde ésta se encontrara. Si se trataba de leña de árboles trasmochos (alcornoque, castaño, quejigo, encina) se cortaba el árbol por el tronco y una vez en el suelo se podaban las ramas y se troceaba el tronco. En el caso de que utilizara leña de rama (jaras, enebros), se procedía a eliminar las puntas y ramas delgadas inservibles para la obtención del carbón.
Ahora había que elegir y preparar el suelo destinado a la elaboración del carbón, siendo su forma, más o menos, circular. El suelo del horno había que compactarlo mediante el apisonado de la tierra para imposibilitar la entrada de aire a través del mismo, ya que si existieran corrientes sería muy difícil controlar el fuego durante la carbonización. Una vez limpio el suelo y colocada la leña en los alrededores comenzaba la fase de armado del horno. En primer lugar, se clavaba un palo verticalmente en el centro del ruedo. En segundo lugar, se colocaba la leña alrededor del palo formando un cono y procurando que quedara uniformemente distribuida para que de este modo se redujera el número de grietas durante la cocción.
Sobre el horno se colocaba una capa de helechos, hierba, musgo u hojarasca. En este momento se procedía a la extracción del palo que se había colocado en el centro y se taponaba el agujero (futura chimenea) para impedir la entrada de tierra de la última capa. La cubierta es la que aísla la madera del exterior para que el oxígeno del aire no la incendie. La correcta carbonización no es más que la combustión lenta e incompleta de la madera por falta de oxígeno.Cerca del horno se encendía una pequeña hoguera y las brasas obtenidas se iban introduciendo a través de la boca del horno. Una vez que el fuego alcanzaba la fuerza suficiente para no extinguirse se tapaba la chimenea. En este punto se procedía al tapado de la chimenea, primero con helechos y más tarde con tierra. A partir de ahora la vigilancia debía ser exhaustiva, sobre todo, durante las primeras diez horas, momento en que comenzaba la carbonización de la corona. Durante la carbonización la leña iba perdiendo volumen por lo que había que golpearla y de esta forma compactar el carbón ya hecho y reducir los huecos que se producían.
Si la cocción era demasiado rápida, el carbón se quemaba, obteniéndose carbonilla. Si la cocción era demasiado lenta, el carbón tendrá zonas mal cocidas, consiguiendo tizos (leña de carbonización incompleta). Por estas razones, el carbonero tenía que abrir agujeros de ventilación en aquellas partes con menor temperatura y taponar las zonas con mayor temperatura, procurando alcanzar una intensidad homogénea del fuego en las diferentes alturas del horno. La carbonización se desarrollaba de arriba a abajo y del centro hacia la superficie. El tiempo de duración de este proceso variaba en función del tamaño del horno, rondando la semana. Una vez terminada la cocción se procedía a apagar y enfriar el horno para lo cual se removía la tierra quemada con el fin de cerrar los poros de ventilación y así apagar los pequeños focos de fuego que todavía quedaran en el interior. Tan sólo resta el envasado y transporte del carbón. El envasado era realizado por los propios carboneros, para tal fin se hacía pasar una cuerda a modo de pespunte por el perímetro de la boca del saco. Para terminar portaban los sacos a hombros y los llevaban hasta el cargadero. El transporte más utilizado eran las bestias de carga que conducidas por arrieros llevaban el carbón a sus lugares de destino.
El martinete aparece en la documentación en la segunda mitad del siglo XVII. Perteneció primero a D. Pedro Jacinto de Vega Loaysa (Caballero de la Orden de Santiago) y después, ya en el siglo XVIII, al monasterio de religiosas de San Bernardo de la Villa de Talavera. (Convento de San Bernardo. Convento de clausura de las madres bernardas, de estilo barroco fundado en 1610 por doña Teresa Saavedra). Siempre se explotó en arrendamiento. El propietario cedía, a cambio de la renta contratada, la vivienda, las fincas de alrededor, el martinete, las herramientas, etc… Los renteros eran por lo general varios vecinos de Arroyo Castaño de Mombeltrán, que se comprometían a reponer lo que se gastaba o destruía y que trabajaban generalmente sirviéndose de un martinetero asalariado, algunos encopadores y otros mozos jornaleros. Trabajaban mil ochocientos quintales de cobre al año y producía más de cuatro mil reales. Fabricaban calderos y calderas de distintos tipos y tamaños, a veces por encargo, que se comercializaban ordinariamente en las comarcas y pueblos cercanos. En 1669 fabricaron una caldera destinada a un tinte de la villa de Bejar, lo que demuestra su prestigio en otros lugares más lejanos. Su actividad se mantendría hasta el siglo XIX.
Un día los viejos calderos de cobre fueron arrinconados para dar paso a otros artilugios. Hoy lo que queda del viejo Martinete permanece a la orilla del río Ramacastañas y cada día que pasa es engullido un poco más por la vegetación de ribera. Algunas noches el rumor del agua nos trae las notas lejanas del martinete al golpear sobre el yunque. Lastima que no sepamos, mas bien no queramos, encontrarle una utilidad que bien podría ser convertirlo en aula de Naturaleza a fin de que los niños de la comarca puedan entender un poco mejor el pasado de su tierra.
Documentación utilizada:
Mombeltrán "Historía de una villa señorial" - Eduardo Tejero Robledo
Mombeltrán y su historía - Gonzalo Martín Garcia
-www.sierranieves.com
-www-sasua.net